Les démarches et les outils pour réduire les coûts de maintenance
Avis d'expert de Sébastien Chen sur la réduction des coûts de maintenance
Article paru dans Maintenance & Entreprise n° 662, Mai / Juin / Juillet 2021
Spécialiste du conseil en management depuis plus de 30 ans, Quaternaire accompagne les ETI et Grandes entreprises, dans des projets d'amélioration durable de leur performance industrielle. De la co-construction d'un projet sur-mesure jusqu'à l'accompagnement opérationnel terrain, Quaternaire intervient sur l'ensemble des leviers de performance industrielle (sécurité, qualité, productivité, supply, ...) et bénéficie d'une expertise reconnue dans les démarches d'amélioration de la performance maintenance.
Des fondamentaux maintenance à la maintenance du futur, Quaternaire accompagne sur le terrain les projets de transformation maintenance en agissant sur les processus, l'organisation et le développement des compétences, en plaçant le management opérationnel au cœur de son accompagnement et en faisant du digital un véritable levier de performance.
Réduisons les coûts de maintenance ! Un propos que l'on entend très fréquemment dès lors que l'entreprise recherche des économies pour tenter de rester dans la course. Malgré tout, il ne faut pas « simplement » se dire « nous allons réduire le budget de maintenance de 10% ». Avant tout, nous aimons rappeler que les coûts de maintenance sont de 2 natures : les coûts directs et les coûts indirects. Le budget de maintenance est souvent perçu comme un centre de dépenses important qui ne créé pas de valeur, et donc rester la cible n°1 des optimisations... alors que les coûts indirects sont la partie immergée de l'iceberg et que ces coûts sont bien plus importants que le budget seul de la maintenance.
Mieux cibler les dépenses maintenance !
les coûts directs, communément appelé le « budget de maintenance », comprennent : les coûts de main d'œuvre interne, les pièces détachées, les prestations externes ainsi que les entretiens exceptionnels.
Avant de lancer une « chasse aux coûts », il est important de se poser la question suivante « mon budget est-il correctement dimensionné ? ». Pour vous guider et vous positionner, nous disposons d'éléments de benchmark par secteur. Par exemple, le poids économique de la maintenance = budget maintenance / valeur à neuf des équipements doit être compris entre 3,5% et 5% pour les industries de transformation ou de conditionnement.
Une fois cette étape réalisée, lancer une analyse de criticité VIS des équipements (Vitaux - Importants - Secondaires) [Schéma 1] permet de focaliser l'énergie et les ressources sur les « bons » équipements. Certes cette méthode n'est pas nouvelle, mais bien cadrée et menée avec les équipes maintenance et production, elle permet d'orienter les actions de maintenance préventive, la gestion des stocks, les choix budgétaires et leur pilotage.
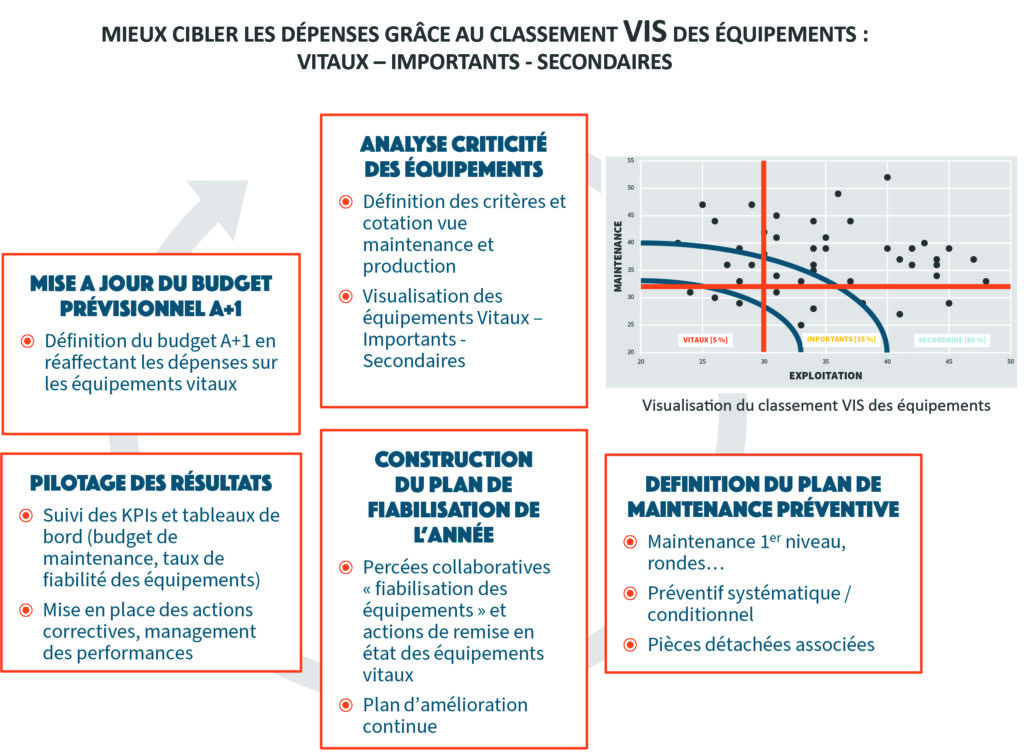
L'expérience montre que les 1ers effets directs/visibles sur la répartition des coûts de maintenance sont :
- Une diminution drastique des plans de maintenance préventive sur les équipements non critiques, comme le montre l'exemple réel du schéma 2. L'analyse VIS des équipements réalisée en 2017 a eu des effets sur les 2 années qui suivirent : baisse des heures de préventif, sans augmentation du correctif. Et une nette augmentation des activités d'amélioration des équipements, et une réduction de 10% sur les prestations externes et pièces détachées.
- Une baisse du niveau de stock grâce à la priorisation des achats de pièces sur les équipements critiques / stratégiques.
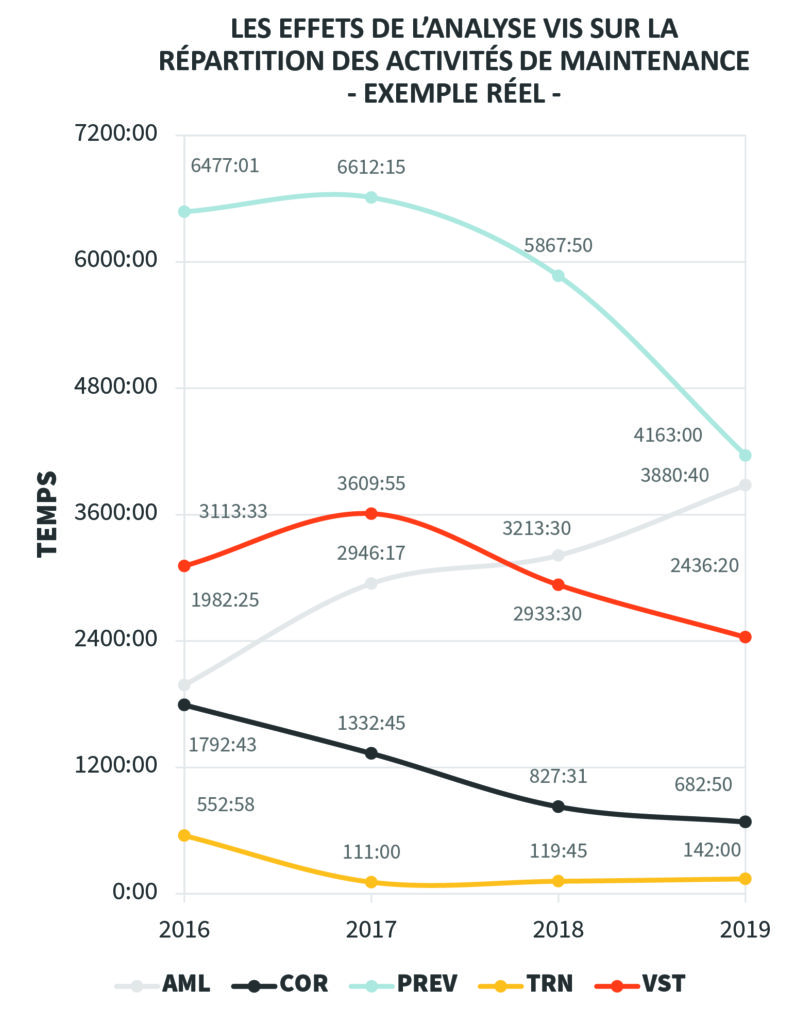
Il convient ensuite de « bien dépenser ». 3 actions à prioriser :
- Le stock de pièce détachée : si vous avez un ratio de Stock/Valeur à neuf supérieur à 1,2 %, alors une des méthodes pour le réduire consiste à uniformiser les pièces en stock, à supprimer les pièces qui ne tournent pas et à mettre des stocks consignataires chez des professionnels. Cela ne fonctionnera que si les règles de sorties, les inventaires tournants sont mis en place et pilotés régulièrement (1 fois par mois mini).
- Les prestations externes : si vous avez un ratio Prestations externes/Budget supérieur à 33%, deux solutions peuvent être envisagées : construire un référentiel de compétences techniques et former les équipes, mettre en place des contrats de maintenance sur les utilités et contrats groupes (les énergies comme air, élec, gaz et froid) afin de recentrer les équipes sur leur cœur de métier.
- Les coûts de préventif : Si vous avez un ratio Heures préventif/Heures totales maintenance supérieur à 33%, installer des contrôles de préventif conditionnel et ne pas faire que du préventif systématique, cela permettra plus facilement de détecter les dérives et d'avoir une meilleure fréquence de changement des pièces plutôt que de les changer systématiquement.
Dimensionner, réorganiser, piloter et animer les performances... les résultats de cette démarche ne sauraient être durables sans clarification des rôles et responsabilités de chacun et sans un pilotage fin des activités et du budget au plus près du terrain. Pour cela, le pilotage des activités et coûts associés doit s'intégrer dans les routines d'animation de maintenance et ne doit surtout pas être un sujet tabou.
Agir sur les coûts indirects
Les coûts indirects sont souvent sous-estimés et pourtant concentrent les dépenses / pertes les plus importantes. Ces coûts indirects totalisent tous les impacts sur la production liés à la non-fiabilité des installations :
- Les pertes de production : hausse des retards de livraison client et des pénalités, dégradation du taux de service, satisfaction client, image de marque...
- La main d'œuvre inoccupée : perte de productivité, climat social dégradé...
- Les pertes matières (matières premières ou produits semi-finis) : perte sèche, puis retraitement, reclassement de produit.
- La non-qualité...
3 leviers incontournables pour agir sur ces coûts indirects :
- Mesurer au plus près du terrain avec les outils de MES et de GMAO (saisir des temps d'arrêts, catégorisation et saisie des interventions réalisées) ;
- Intégrer l'analyse de ces pertes dans des rituels d'animation (Tour terrain, Point d'équipes, Points quotidiens...) ;
- Lancer des sujets de résolution de problèmes et d'analyse de pannes sur les causes majeures de pertes avec les équipes terrains.
Selon le degré de maturité des organisations maintenance, l'intégration de solutions 4.0 peut décupler les performances. Sécurisation de la fiabilité des équipements par la maintenance prédictive, développement de l'auto-maintenance par la réalité augmentée, animation des indicateurs grâce au management visuel digital, création de communautés métier digitales, GMAO mobiles... un bon vers la maintenance du futur qui nécessitera également méthodes et accompagnement opérationnel sur le terrain.
Pour pouvoir accéder à l'ensemble des articles, abonnez-vous à Maintenance & Entreprise : www.maintenance-entreprise.com
Nos dernières actualités
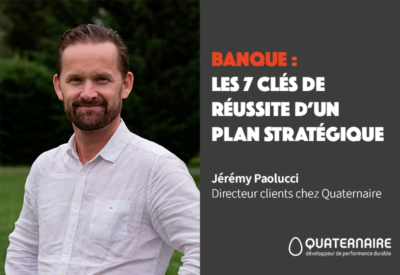
Banque : les 7 clés de réussite d’un plan stratégique
Dans un contexte de transformations économiques, sociales et technologiques accélérées, le plan stratégique ne peut plus être un simple document de cadrage. Il doit devenir un récit collectif, partagé et vivant, qui aligne vision, action et engagement. À travers 7 clés concrètes – du diagnostic partagé à l’animation continue – cet article explore les leviers essentiels pour concevoir et déployer un plan stratégique durable, capable d’embarquer l’ensemble des parties prenantes.
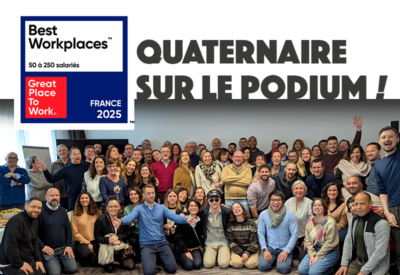
Quaternaire sur le podium des Best Workplaces 2025 !
Quaternaire se hisse sur le podium des meilleures entreprises où il fait bon travailler en 2025. Cette avancée reflète un engagement collectif fort, des initiatives concrètes et un management de proximité, au service du bien-être et de la performance durable.
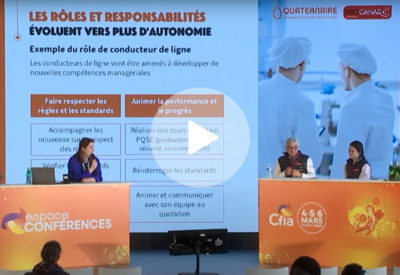
[Replay] Témoignage de Procanar : Modernisation et transformation des métiers techniques et managériaux
Procanar transforme son site et ses métiers ! Avec Cap Houad, l’entreprise allie modernisation industrielle, montée en compétences et management de terrain. Un retour d'expérience de Manuel Machado et Marie-Elise Garnie à découvrir en vi