Continuous improvement, cement of Knauf Group
Being a benchmark in customer satisfaction is now a sine qua non for any company wishing to stay one step ahead. All the more so in today's ever-changing competitive markets. The Knauf Group has understood this and has made customer satisfaction its No. 1 concern by committing all its forces - 35,000 employees worldwide, in more than 250 plants - to a renewed drive for progress.
When a company is located all aroud the globe, its success often lies in its ability to unite people around a common goal. In response to this major challenge, the deployment of a multi-site operational excellence approach also contributes to achieving crucial objectives for the company: improving SQCDME performance (safety, quality, costs, deadlines, motivation, environment) in a sustainable and proactive way, forging a common culture between sites or involving employees 100% to increase, motivate, recruit and retain...
Start with a pilot site before a multi-site roll-out...
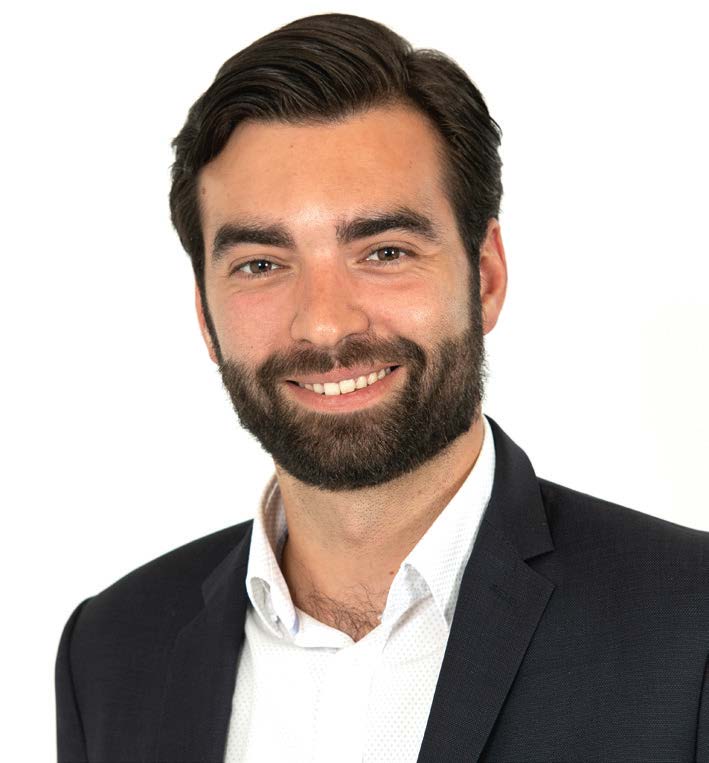
This is demonstrated by the deployment of the Continuous Improvement (CI) project within several of the group's entities, including Knauf Weila (Western Europe, Israel & Latin America). “In order to develop a vision and improve its structure, the Knauf Group is fighting a number of strategic battles", explains Benjamin Lardé, CI manager for the area covering Western Europe, Israel and Latin America. "Aiming to reach new levels in terms of product quality, meeting deadlines and price competitiveness, the continuous improvement approach has, for the past 2 years, enabled us to deploy this strategy in the field and across our geographical perimeter, which includes 23 sites.”
This was a far-reaching transformation that required a great deal of support. “Because we recognized their hands-on approach, coupled with pragmatic management methods and tools, we chose to embark on this project with Quaternaire” explains the CI manager. In 2019, the partnership will get under way at an initial pilot site: Knauf Plâtres in Saint-Soupplets, near Marne-la-Vallée (77 - France), with the aim of jointly developing the stages of the approach. Following a diagnosis to identify the ‘irritants’ in the processes, a roadmap was drawn up prioritizing the various improvement projects to be carried out according to their purpose and degree of priority. When the project is launched, 20 improvement projects are planned.
Structuring and winning fast!
As part of the CI project, a number of project have been launched to generate direct gains and others to provide structure. With the choice of balancing them. In this type of strategie transformation, it is essential to obtain the first visible results quickly, while guaranteeing the sustainability of the gains achieved. Without rapid gain, the approach will not work, with the risk of a tunnel effect for the teams.
Looking only for quick wins can, on the other hand, lead to a blow-out effect. In its roadmap, Knauf Weila has therefore set out to combine structuring projects (organization, short-interval management, maintenance methods, key processes, etc.) and projects with direct benefits, such as reducing production changeover times. "To meet strong market demand, we had to reduce the transition times for series changes as much as possible," explains Benjamin Lardé. "Using the SMED (Single Minute Exchange of Dies) method, we reduced production changeover times on the plasterboard line at Saint-Soupplets. This has generated several thousand euros in savings, satisfaction among employees, who feel more responsive in their work, and ultimately customer satisfaction."
The project as a whole has already generated savings of €300k and enabled 200 irritants to be dealt with on the ground, via collaborative projects. These projects are aso synonymous with skills development for the teams. Working closely with the production lines to help Knauf's team grow, Quaternaire has also implemented a training program. The result is a foundation of shared managerial practices!
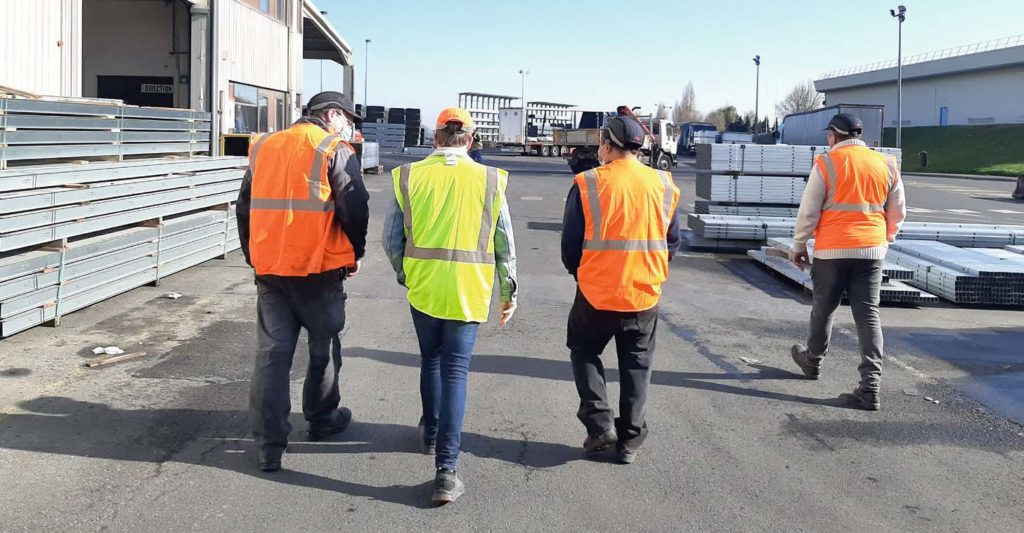
Operational excellence beyond borders
Bringing men and women on board the same train of progress, the CI approach is now spreading to all knauf Weila's industrial sites. Each site is being rolled out over a 3-year period, from the introduction of the fundamentals (managerial rituals, performance management and steering, etc.) to the complete empowerment of the teams. "With the help of Quaternaire, chich regularly carries out international multi-site projects, we have tested remote support for a self-maintenance project and training in Argentina in 2020. A conclusive POC (Proof of Concept) that opens up other prospects for us", concludes Benjamin Lardé. In France, Belgium and beyond, the quest for excellence is becoming the cornerstone of a solid, galvanizing corporate culture.
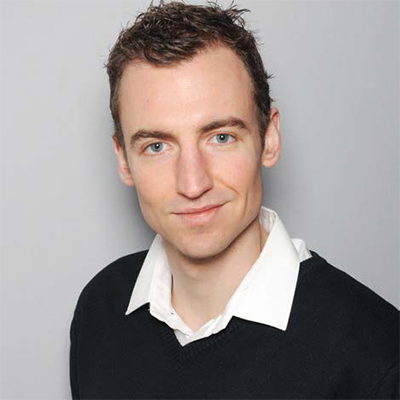
Reducing drudgery and maximizing customer satisfaction
Jérémy Coulm, Director of the Knauf ISBA site in Auxerre, France (42 employees)
“Launched at the beginning of 2021 at our site, the CI approach has enabled us to carry out a complete diagnosis of our processes and tools, to discuss the irritants encountered and to prioritize future actions according to the gains targeted (quality performance, QWL, etc). For example, we were able to optimize the use of a release agent applied to the molds of our insulating panels. Over time, we noticed drifts on the line, leading to an increase in customer complaints and more cleaning of the mod and/or its environment. We therefore worked to find the right balance between under-and-over-consumption of this release agent. This project has made the task less arduous for the operators, who no longer have to scrap the mold as much at the end of production. It has also helped to maximize customer satisfaction. Now that the best practices have been identified, we just need to anchor them in the long terme."
Knauf Group
- Activity: Production of builiding materials and systems
- Implantation: 250 production sites in over 90 countries
- Number: 35,000 employees
- Turnover: €11 billions in 2020
Front page!
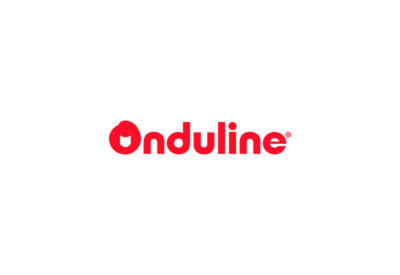
Onduline France transforms its customer service
Onduline France optimizes its processes and reorganizes its customer service for greater customer satisfaction. A look back at a collaborative project carried out with its employees.
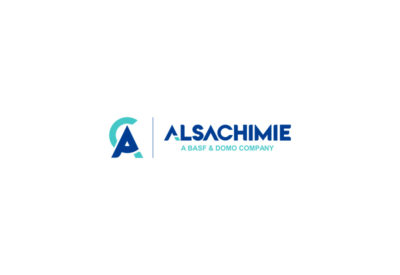
Alsachimie: Putting "behaviors and attitudes" at the heart of the strategy
Alsachimie, a leader in the chemical industry, places behaviors and attitudes at the core of its strategy through an innovative framework, derived from the company's values and shared with all its employees.
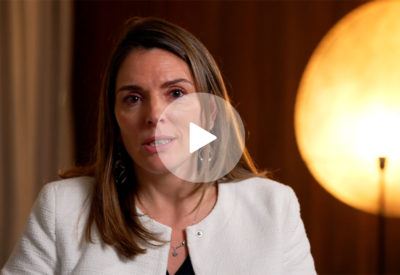
Elivia: HR Deputy Director's testimony
Catherine Chalumeau, HR Deputy Director, discusses the "Management by Elivia" project, intended to establish a lasting managerial culture