Socomec: a solution for building a shared quality culture
Socomec, a company offering innovative solutions dedicated to the performance of electrical installations, has set itself the goal of prioritizing collective rather than individual benefits. The group has decided to equip its 13 sites with the collaborative digital solution Fabriq. From standardization of practices and implementation of the solution, to operational support for teams, we take a look back at 4.0 transformation project focused on 100% customer satisfaction, with Thierry Mathien, Group Quality Director.
In search of a new synergy
For Thierry Mathien, Socomec's Quality Director, this standardization project is the result of "increasing customer requirements for increasingly complex products, coupled with cost issues. On close as possible to our customers. A switch that meets both environmental imperatives and a strengthening of the company's overall performance."
"To create synergies, we had to find a solution that could connect all the sites together, and cirulate information in real time to enable teams to react quickly to any deivations in performance", he adds.
The situation was simple: the group has 13 factories on each continent, with different maturities and management tools. We quickly opted for a standard solution that would meet four key challenges:
- Operating in all plants, whatever their size (from 30 to 500 people... in China, India, Italy, France, Tunisia, USA...)
- Using the solution without the help of a translator
- Integrating all the tools of Socomec's production system (the SPMS)
- Enabling easy communication between each site
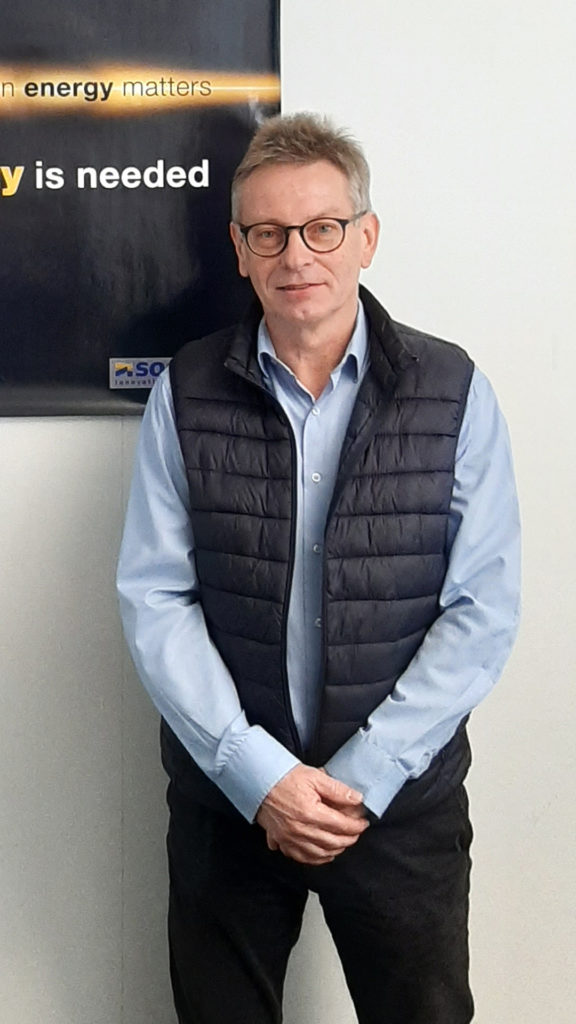
After evaluating various digital solutions, a partnership was formed with Fabriq, and Socomec called on Quternaire to ensure its successful deployement to its teams.
The Key for success
To make this project a success, Thierry Mathien list a few key ingredients:
- Defining a common base while guaranteeing the autonomy of each site.
- Testing on small scale before full deployement with a POC (Proof of Concept) on 3 plants and 1 production line.
- Building documentation defining common rules and terminology for 4 concret use cases: ticket management, short interval animation, routine management, problem solving.
- Defining mandatory points (safety, quality, costs, deadlines) and optional points to guarantee autonomy.
- Measuring cultural resistance.
- Building a training plan.
- Communicating regularly to explain the approach.
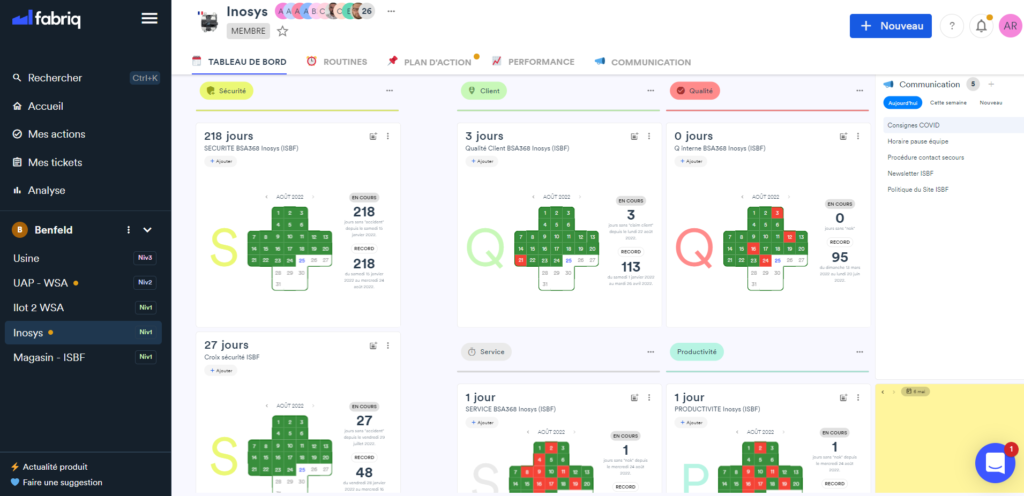
Implanting something new into a daily routine that seems so well established can be met with resistante. "20% of the success of thi approach is dedicated to the platform itsel. The remaining 80% is down to the teams, the work on cultural change and the importance of communication", says Thierry Mathien.
Between fun, visual and educational training, communications and explanations: all the ingredients are brought together to take control of the solution and modify the vision that teams may have had, by insisting on the benefits to be gained. All with one watchword in mind: "Prioritize collective benefits over individual ones, to win teams over with a common base", sums up Thierry Mathien.
Today, Socomec is entering a more global deployment phase for the solution. The aim is to equip 7 plantes by 2023.
Promising results
The project is very recent, but initial successes are already visible. The main benefit is a significant time saving thanks to the speed and efficiency with wich inter- and intra-plant information is transmitted. enabling better dissemination of information. "Between 2 days and 1 week are saved! Gaining in speed and quality is a guarantee of greater customer satisfaction, and this is made possible by real-time activity management, based on shared indicators!" explains Thierry Mathien.
He notes time savings in administrative processes thanks to the automation of certain procedures: "Teams save between 15 and 20 minutes a day by no longer updating indicators manually".
Finally, he observes a change in mindset on the part of the teams, thanks to the introduction of routines, for example ("OK start-up"), with questions linked to safety or quality. "Through the system, we force this acculturation, with the result that employees are on board", remarks Thierry Mathien.
This standardization within the Group's factories is part of the common quality requirement, because "it is thanks to the deployment of common standards and daily support for our teams that we will be able to forge the Group's long-terme competitiveness".
Focus on the deployment of Fabriq by Socomec
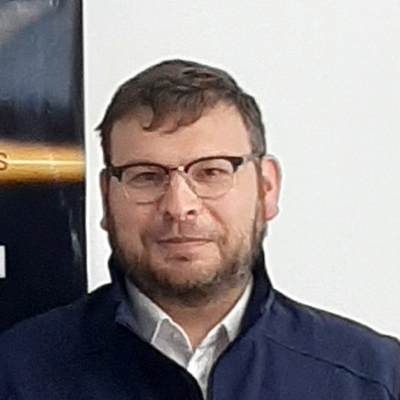
Saving time and collective efficienvy
Guillaume Bein, Project Manager Fabriq by Socomec
"Deploying Fabriq on our industrial sites was a real challenge. It's the first time we-ve done it on all our sites. To do this, we defined a battle plan with a project charter indicating the global orientations. Each site has a sub-project associated with it, with a defined model indicating the steps to be followed and all the documentation to be used by our local Fabriq ambassadors.
From problem-solving to monitoring action plans, from the introduction of routines to improve management, the benefits of Fabriq are manifold. Thanks to the centralization of all our tasks, their planning and execution, we've eliminated a large number of unwanted files and are saving a lot of time!"
Socomec
- Activity: Manufacturer of innovative solutions dedicated to the performance of electrical installations
- Creation: 1922
- Implantation: 12 industrial sites
- Number: 3,900 experts in 28 subsidiaries worldwide
- Turnover: €604 M in 2021
Front page!
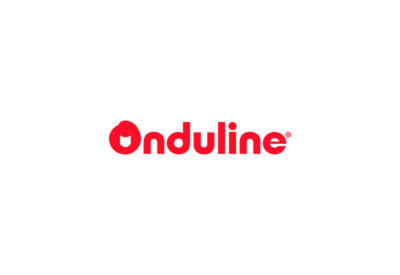
Onduline France transforms its customer service
Onduline France optimizes its processes and reorganizes its customer service for greater customer satisfaction. A look back at a collaborative project carried out with its employees.
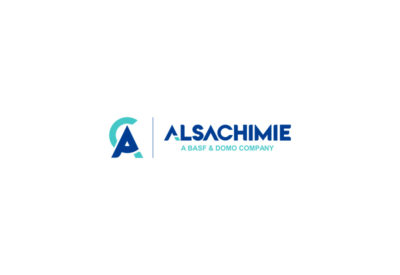
Alsachimie: Putting "behaviors and attitudes" at the heart of the strategy
Alsachimie, a leader in the chemical industry, places behaviors and attitudes at the core of its strategy through an innovative framework, derived from the company's values and shared with all its employees.
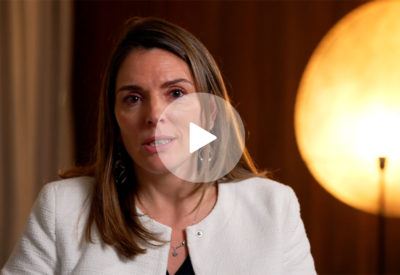
Elivia: HR Deputy Director's testimony
Catherine Chalumeau, HR Deputy Director, discusses the "Management by Elivia" project, intended to establish a lasting managerial culture